旋盤加工者であれば誰もが経験する「びびり振動」。以前の記事では、その原因を分類し、現場で即座に取れる実践的な対策を解説しました。
しかし、熟練の技術者であれば、こう感じたことがあるはずです。 「なぜ、回転数を変えるとびびりが止まることがあるのか?」 「なぜ、突き出しを短くすると効果的なのか?」 「そもそも、この振動の正体は何なのか?」
この記事では、一歩踏み込んで、びびり振動の発生メカニズム(しくみ)に迫ります。古典的な研究が解き明かした「共振」のメカニズムと、昔ながらの職人の知恵、そして現代の技術がどうびびりに立ち向かうのか、私の言葉で分かりやすく解説します。
この「なぜ」を理解することで、あなたのびびり対策は、経験則から理論に裏打ちされた確かな一手へと進化するはずです。
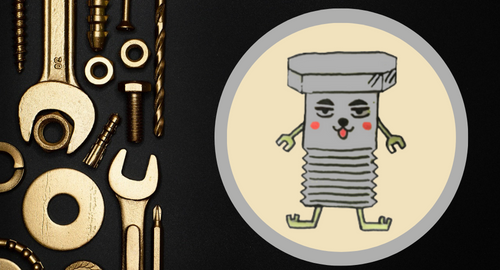
- 旋盤歴22年(汎用、半NC、NC旋盤、C陣制御の複合加工機)
- 旋盤屋を経営
- 自動車、製鉄、航空機、工作機械、半導体などの単品仕事で営んでおります
- 加工の奥深さに日々精進
- 本ブログでは、私が勉強してインプット、アウトプット用に作成しています。細心の注意を払っておりますが、間違いがある場合があるのでよく確認してください。
H2: びびりの本質は「共振」にあり――古典的研究が解き明かしたメカニズム
びびり対策を語る上で避けて通れないのが、「共振(きょうしん)」という物理現象です。これは古くからびびりの主要因として知られています。
共振とは? 全ての物体には、揺れやすい特定の周期(固有振動数)があります。この固有振動数と、外部から加わる力の周期が一致したときに、揺れ(振動)が急激に増大する現象です。ブランコをタイミング良く押すと、どんどん揺れが大きくなるのと同じ原理です。
旋盤加工におけるびびりも、この「共振」で説明できます。切削中に発生する切削力の周期的な変化(加振力)が、「ワーク」「工具」「機械本体」のいずれかの固有振動数と一致したとき、びびり振動として現れるのです。
1. 工具の自然振動との共振
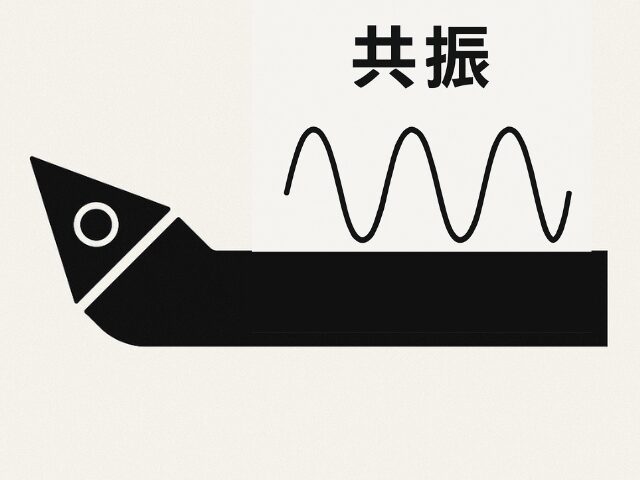
突き出したバイトが「ビーン」と震える現象です。
- 発生しやすい条件: 工具の突き出しが長い、切削速度が速い、切り込みが浅すぎる場合。
- なぜ切り込みが浅いとびびるのか?: 切り込みが非常に浅い状態、特に刃先の丸み(ホーニング)と同程度かそれ以下になると、刃先は材料をスムーズに「切削」できず、表面を「こする」ような状態になります。この状態では、刃先がワークに食い込もうとする力と弾かれる力が交互に働き、切削抵抗が不安定に変動しやすくなります。 この周期的な力の変動が、工具の固有振動数と一致すると共振を引き起こし、びびりにつながるのです。
2. 旋盤サドルの自然振動との共振
刃物台やサドルといった、機械の一部がガタガタと震える現象です。
- 発生しやすい条件: 切削抵抗が大きくなるような加工(切削角度が大きいなど)。
- メカニズム: 機械本体も、その構造や質量に応じた固有振動数を持っています。特に摺動面の油膜やわずかなガタは、ばねのように働き、特定の条件下で切削力の変化と共振することがあります。
3. ワーク(被削材)の横振動との共振
細長いワークが「たわむ」ように大きく振動する現象です。
- 発生しやすい条件: 細長いワーク(特にL/D比が大きいもの)を加工する場合。
- メカニズム: ワーク自体も固有の振動数を持ちます。特に細長い棒材は、ギターの弦のように横方向に振動しやすく、切削力の変化と共振して大きなびびりを引き起こします。ワークの中央部で振幅が最大になるのは、まさにこのためです。
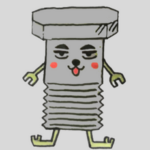
経験上、ワーク径の10倍を超えるようですと、振れ止め使う段取りを考えます
びびり対策の進化:伝統の知恵から次世代技術まで
これまでのびびり対策は、「剛性を高めて共振を避ける」という考え方が主流でした。しかし、それだけでは解決できない問題に対し、様々なアプローチが生み出されてきました。ここでは、伝統的な知恵から最新技術まで、3つの異なるアプローチを紹介します。
アプローチ①:力の「発生源」で方向を変える(ヘールバイト)
ヘールバイトは、すくい角や横切れ刃角といった「刃先の形状」そのものを工夫することで、発生する切削抵抗のベクトル(方向)を変えます。ワークの中心に向かう力(背分力)を小さくし、接線方向の力(主分力)に変換することで、ワークを揺らす原因となる力を根本から減らし、びびりを抑制する伝統的な対策です。
アプローチ②:「コシを弱くして」力の伝わり方をずらす(職人の知恵)
一見すると逆効果に思える「あえて工具のコシを弱くする」という対策も、昔からの職人の知恵として存在します。これは、「工具ホルダー(シャンク)の構造」を工夫して、力の伝わり方をコントロールする考え方です。
分かりやすい例:ブランコの例え
- びびりの発生: ブランコが前後に揺れているところに、タイミングを合わせて真後ろから押すと、どんどん揺れが大きくなります。これが「共振」です。
- 職人の知恵: では、ブランコを揺らしている最中に、真横から押してみたらどうでしょう? うまく力が伝わらず、ブランコの揺れはむしろ収まってしまいます。
この「力を加える方向を、揺れやすい方向から意図的にずらす」というのが、この知恵の核心です。
工具ホルダーの一部だけを柔らかくすることで、力の揺れが伝わる方向を変化させ、ワークが揺れやすい方向との「ミスマッチ」を生み出し、びびりの成長を抑制します。
アプローチ③:振動そのものを「吸収」する(次世代技術:防振ボーリングバー)
そして、現代のびびり対策の切り札とも言えるのが、ダンパーを内蔵した「防振ボーリングバー」です。これは、特に突き出しの長い内径加工で絶大な効果を発揮します。
なぜ「ダンパー」がびびりを劇的に抑制するのか?
この技術の鍵は、振動エネルギーを「吸収して熱に変える」という、制振(せいしん)の考え方にあります。
分かりやすい例:自動車のサスペンション
- ばねだけの場合: 自動車のサスペンションにばねしか無かったら、段差を乗り越えた後、車体はいつまでもフワフワと揺れ続けます。
- ダンパー(ショックアブソーバー)がある場合: ばねと一緒にダンパーが付いていることで、段差を乗り越えた後の揺れを「スッ」と一回で収束させます。
防振ボーリングバーは、このダンパーの役割を工具内部に持っているのです。
ボーリングバーの内部には、重り(ウェイトマス)が特殊なゴムや油などの減衰材を介して組み込まれています。
- 工具がびびり始めると、内部の重りはその振動と逆の動きをしようとします。
- この「工具本体」と「内部の重り」の動きのズレが、減衰材によって抵抗となり、振動エネルギーが熱エネルギーに変換されます。
- 発生した振動が瞬時に吸収・減衰されるため、共振による振動の増大が起こらず、安定した加工が可能になるのです。
特に、突き出し長さが工具径の7倍、10倍といった、通常では加工が困難な深穴加工において、この防振ボーリングバーは唯一無二の解決策となる場合があります。
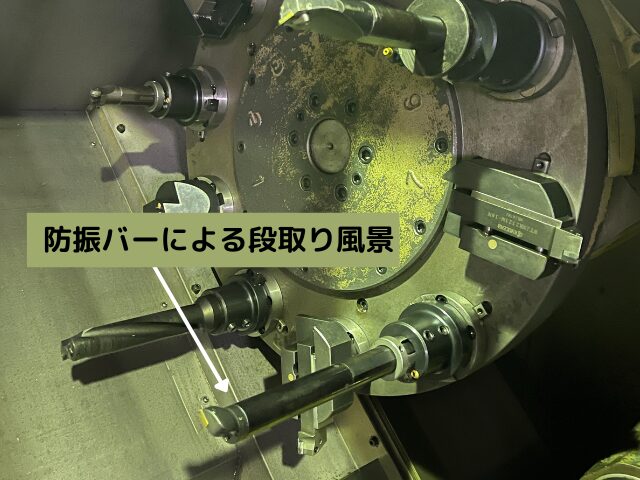
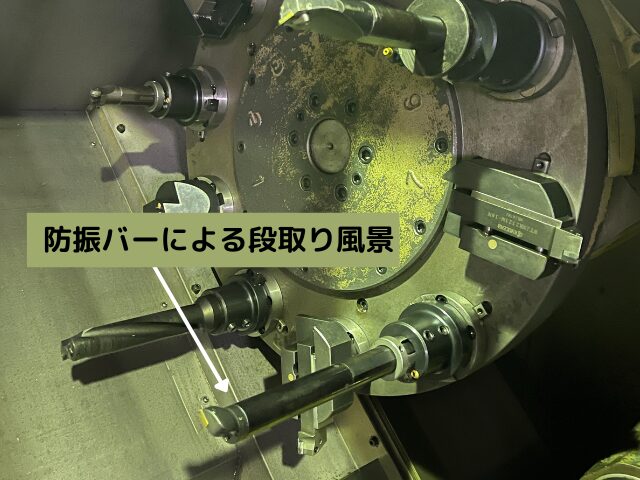
理論から実践へ:あなたのびびり対策をアップデートする
では、これらの理論を知ることで、私たちの日々の対策はどう変わるのでしょうか。各対策がなぜ有効なのか、物理的な視点からより深く理解してみましょう。
- 「突き出しを短くする」「太いシャンクを使う」のはなぜ? → これは工具の剛性を高める行為です。物理的に、物体の固有振動数は剛性の平方根に比例します 。つまり、剛性を高めると固有振動数も高くなります。これにより、通常の切削で発生する加振力の周波数域から固有振動数が外れ、共振しにくくなるのです。
- 「振れ止めやセンターで支える」のはなぜ? → 上記と同様に、ワークの剛性を高めることで、ワークの固有振動数を高くし、共振を回避するアプローチです。びびり対策の最も基本的な考え方と言えます。
- 「ノーズRを小さくする」「すくい角を大きくする」のはなぜ? → これは切削抵抗、特にびびりの主因となる背分力を直接的に小さくするための対策です。ブランコの例えで言えば、タイミング良く押すのは同じでも、その押す「力」自体を弱くすることに相当します。加振力のエネルギーが小さければ、たとえ共振点に近づいても振動の振幅を小さく抑えることができます。
- 「切削速度を変える」のはなぜ? → これは切削力の変化の周期(加振周波数)を直接変える行為です。切削速度が変わると、単位時間あたりに刃先がワークと接触し、切りくずを生成する回数が変わります。これが加振周波数の変化につながります。共振は「加振周波数 = 固有振動数」の時に発生するため、切削速度を変えることは、この等式を崩す最も直接的で効果的な手段の一つなのです。
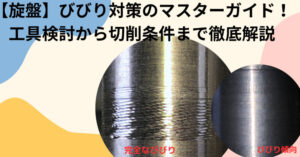
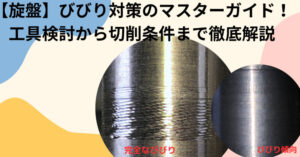
びびり対策の真髄:加工の「上流工程」から考える戦略的アプローチ
ここまでの話は、発生してしまったびびりへの「対処法」でした。しかし、真のプロフェッショナルは、問題が起きてから対処するだけではありません。そもそも問題が発生しにくい状況を、いかにして作り出すかを考えます。
これは、読者の皆様がまだ意識していないかもしれない「潜在的なニーズ」に応える視点です。びびりを制御できる技術力は、単なるトラブルシューティング能力ではなく、「他社にはできない高付加価値な仕事」を受注するための強力な武器となり得ます。
1. 設計段階:加工者目線でのフィードバック
びびりの原因の多くは、ワークの形状に起因します。もし設計者とコミュニケーションが取れる立場なら、加工のプロとしてフィードバックが可能です。
- 「この部分の肉厚をもう少し確保できませんか?」
- 「ここにリブを一本追加するだけで、剛性が格段に上がります」
- 「この公差であれば、びびりを抑えるために特別な工程が必要になり、コストが上がります」 このようなの提案は、設計者にとっても有益であり、あなたの付加価値を大きく高めます。
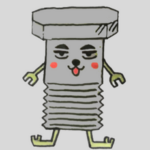
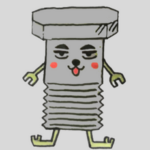
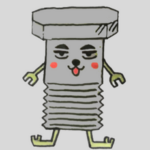
製造容易性設計にするにはかなり高度な信頼関係が必要です。もちろん出来ないことも多いですが、なぜ出来ないかを聞き出すことも勉強になることが多いです
2. 工程設計段階:剛性を維持する加工順序
同じ製品を作るのでも、加工の順番次第でびびりの発生しやすさは全く変わります。
- 剛性の高い部分から加工する: 例えば、細長いシャフトの両端に太い部分があるなら、まずは太い部分を仕上げ、そこを基準に細い部分を加工する。
- サポート部を最後に除去する: 薄肉のフランジなどを加工する場合、びびりの原因となる薄い部分を支える「サポート部」をあえて残しておき、最終工程で除去する。
- 荒加工と仕上げ加工の分離: 荒加工で大きな応力をかけた後、一度チャックを緩めて歪みを取り、再度把握して仕上げる。
これらの工程設計は、びびりを未然に防ぐための戦略そのものです。
3. 工具・治具選定段階:戦略的投資の判断
「防振ボーリングバーは高いから…」と敬遠するのではなく、「この工具があるから、他社が断るようなL/D比の大きな深穴加工が受注できる」という発想の転換が重要です。
- コストと利益のトレードオフ: 高価な工具や特殊な治具への投資が、どれだけの加工時間短縮や不良率低減に繋がり、結果としてどれだけの利益を生むのか。
- 技術的優位性の構築: 「びびりやすい加工」を安定してこなせる技術力は、価格競争から脱却し、高単価な仕事を選ぶための強力な武器になります。
このように、びびり対策を「上流工程」から戦略的に考えることは、あなたの技術力を会社の「収益力」へと直結させるための、非常に重要な視点なのです。
まとめ:職人の勘と物理学の融合
びびり振動は、単なる不快な現象ではなく、「共振」という明確な物理法則に基づいています。そして、その対策は「剛性を上げる」という伝統的な手法に加え、「力の方向を制御する」知恵、さらには「振動を吸収する」技術へと進化しています。
【私の経験談】
私も長年の経験の中で、どうしてもびびりが止まらない加工に何度も頭を悩ませてきました。特に記憶に残っているのは、あるステンレスの薄肉長尺加工です。ありとあらゆる対策をしても微振動が収まらなかったのですが、最後に藁にもすがる思いで、セオリーとは逆に回転数を思い切って上げてみたところ、嘘のようにびびりが収まり、綺麗な仕上げ面を得ることができました。当時は「なぜだろう?」と不思議でしたが、今思えば、それは機械とワーク、工具が作り出す複雑な共振点から、回転数を変えることでうまく「脱出」できたのだと、理論的に理解できます。
もちろん、私たちがいきなり特殊なシャンクを設計したり、防振バーを常に使えるわけではありません。しかし、びびりの本質が「共振」であり、その対策には複数のアプローチがあることを理解すれば、「今は何と何が共振しているのか?」を意識し、より論理的に対策を組み立てることができます。
「回転数を変えてみようか」「もう少し切れ味の良いチップにしてみようか」
その一つひとつの選択が、物理法則に基づいた的確な一手となる。 熟練職人の「勘」や「経験」と、こうした物理学的な裏付けが融合したとき、私たちの技術はさらに高い次元へと到達するはずです。
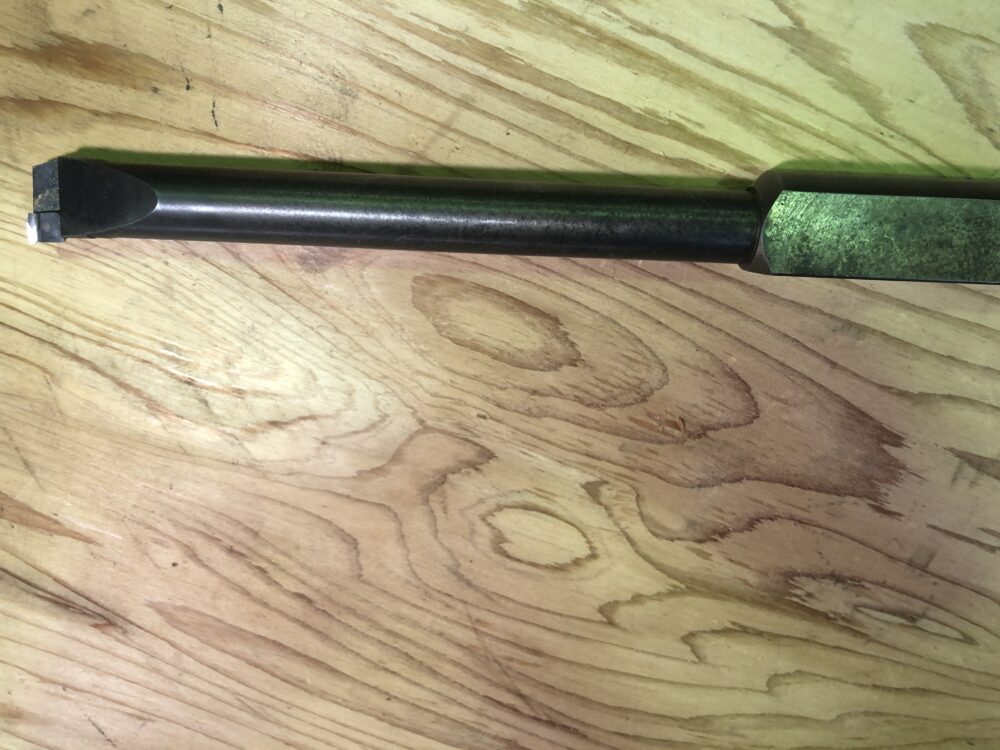
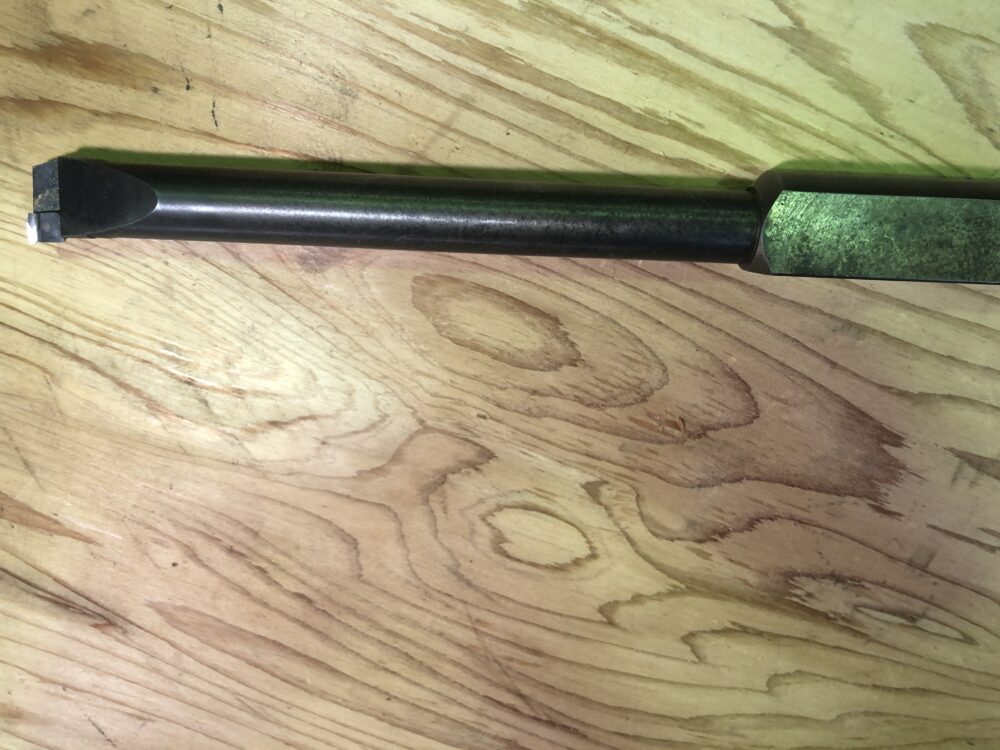
コメント