旋盤の内径加工は様々な問題が絡まってきて、難易度は外径、端面切削よりも難しいです。
この記事では内径加工をするための手順からびびりの対処法、切りくず処理などを紹介いたします。
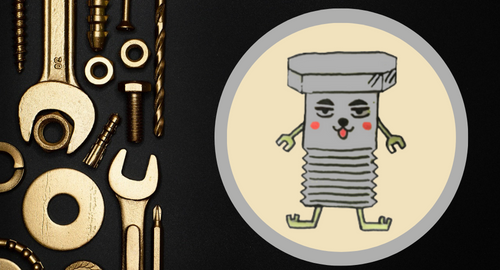
- 旋盤歴22年(汎用、半NC、NC旋盤、C陣制御の複合加工機)
- 旋盤屋を経営
- 自動車、製鉄、航空機、工作機械、半導体などの単品仕事で営んでおります
- 加工の奥深さに日々精進
- 本ブログでは、私が勉強してインプット、アウトプット用に作成しています。細心の注意を払っておりますが、間違いがある場合があるのでよく確認してください。
1.旋盤の内径加工とは
旋盤の内径加工とは、旋盤を使って材料の内側を削る加工方法のことです。ドリルなどで開けた穴を大きく広げたり、内側の表面をきれいに仕上げたりすることが出来ます。
外径加工より、目視出来ないことや切りくずの処理などの原因から、難易度は外径加工より高いです。中ぐり、ボーリングと言う人もいます。
内径加工において、加工法の手順、適切な工具の選定は重要です。工具の選定は、加工する材料、穴のサイズ、仕上げの有無などから考える必要があります。
1.1.内径加工した製品の用途
- ナットの穴、ねじの加工
- 部品の重量を軽くするために穴を大きくする
- 部品の摩擦抵抗を減らすために表面を滑らかにする
- ベアリングを嵌め合わせる
- 軸に焼き嵌めする
・・・・・etc
1.2.内径加工の基本的な種類
内径加工するときの種類(工程)について詳しく説明します。
- 穴あけ
- 内径荒加工
- 内径中仕上げ加工
- 内径仕上げ加工
- 内径溝入れ
- 内径ねじ切り

1.3.基本的な手順
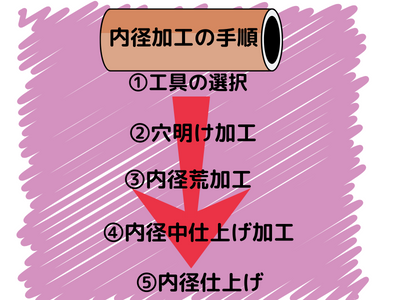
内径加工は一般的に次の基本手順で行います
1.穴加工:
ドリル等で穴をあけます
2.荒加工:
ボーリングバーにチップを取り付けて穴を広げていきます。現場では中ぐりと言ったり、穴を広げるなどと言います。
3.中仕上げ加工:
寸法を出すために中仕上げ加工は重要です。
また、トラブル防止のために荒加工で残ったバリや表面粗さを良くして、穴の表面の状態を整えます。
4.仕上げ加工:
穴の内部表面を平滑に仕上げ、所定の寸法と表面仕上げを達成します。
これらの基本手順で加工することにより、内径加工において高品質な製品を作成することが可能です。
2.内径加工の準備
内径加工を効果的に行うためには、適切な準備をしましょう。工具の選定と切削条件の設定が鍵となります。以下では、内径加工の準備に焦点を当てて説明します。
2.1切削工具の選択
内径加工を行う際、適切な切削工具の選択が重要です。穴のサイズ、加工の仕方、仕上げなどに応じて、適切な工具を選択します。普通の穴を仕上げる際に使用する工具は、ドリルと荒加工用ボーリングバーと仕上げ用ボーリングバーを用意します。
穴加工の工具:
スローアウェイ(チップ)ドリルやスーパードリルやハイスドリルや超硬ドリルなど色々なドリルがあります。
まず最初に取り掛かる工程です。穴の形状とサイズに合わせて、ドリルを選択します。
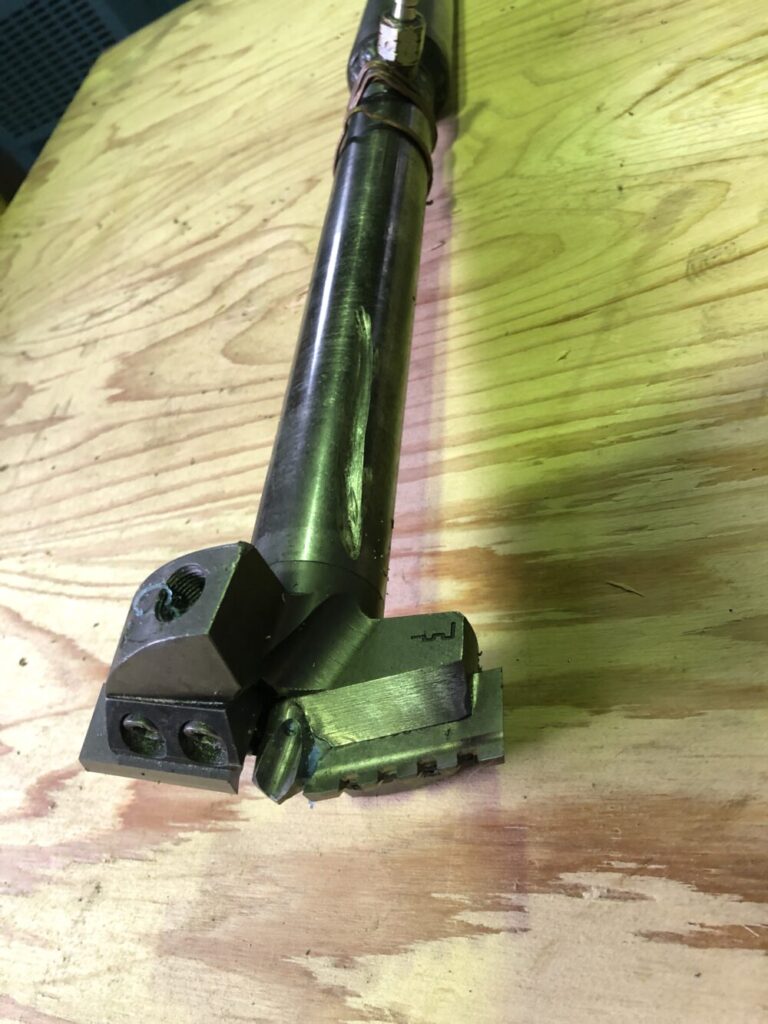
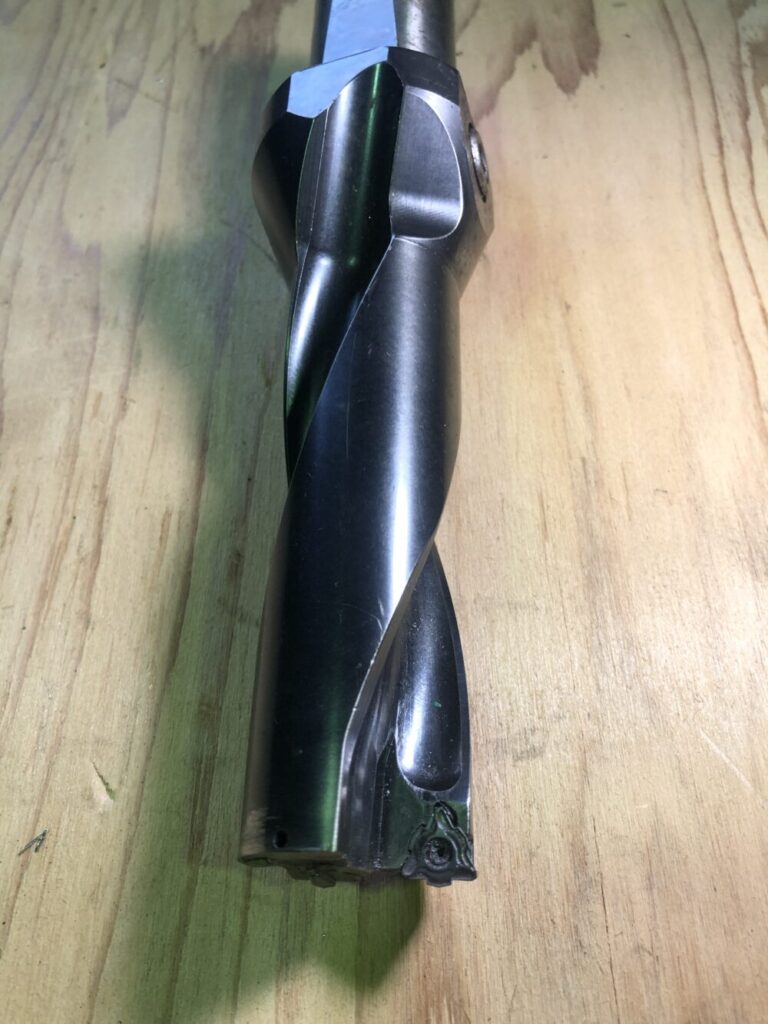
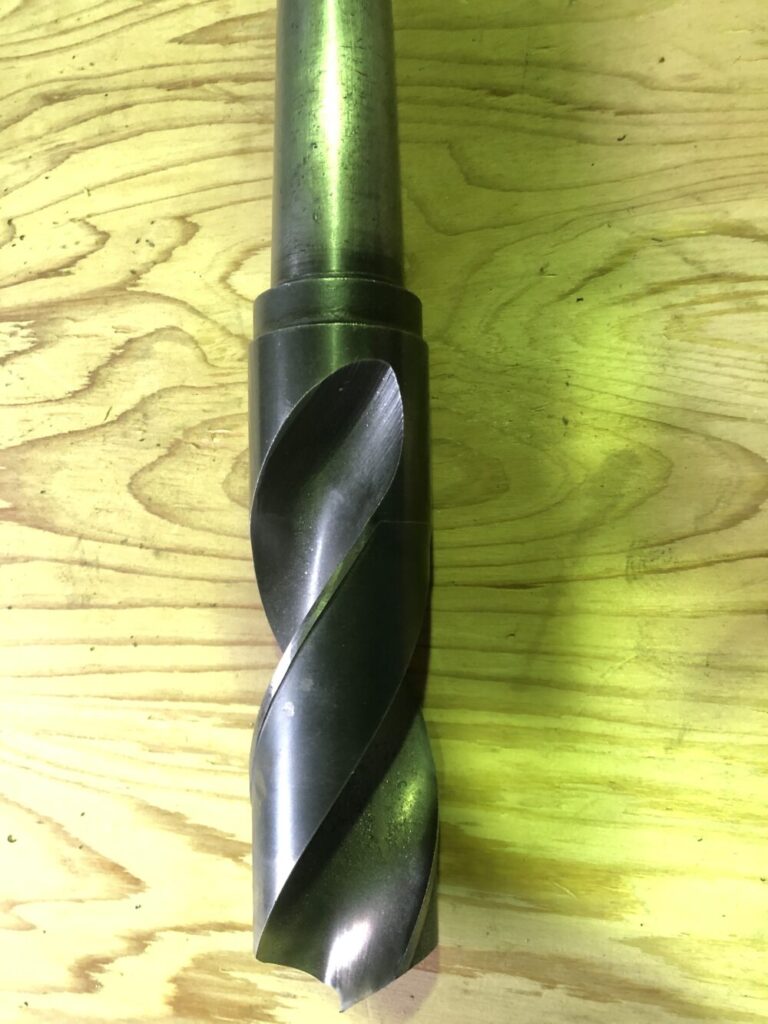
内径加工の工具:
荒加工用と仕上げ加工用の工具(ボーリングバー)が必要です。
使用する工具は加工対象の材料の穴に合わせて選択する必要があります。
荒加工用ボーリングバーも仕上げ加工用のボーリングバーはどちらでも使えます。
では何が違うかと言うと使用するチップを荒加工用と仕上げ加工用で変えます。
あえて荒加工用のボーリングバーと仕上げ加工用のボーリングバーを使い分けるとしたら、
作りがより頑丈なボーリングバーの方のがバリバリ削れます。
穴はドリルで開けておきましょう。
材料に応じてボーリングバーの種類、チップの材質およびチップの形状を選択します。
※内径の加工する深さ(距離)に応じて、ボーリングバーの突き出し量を調節します。
※1穴あけした穴径に応じて、なるべく太いボーリングバーのサイズを選びます。
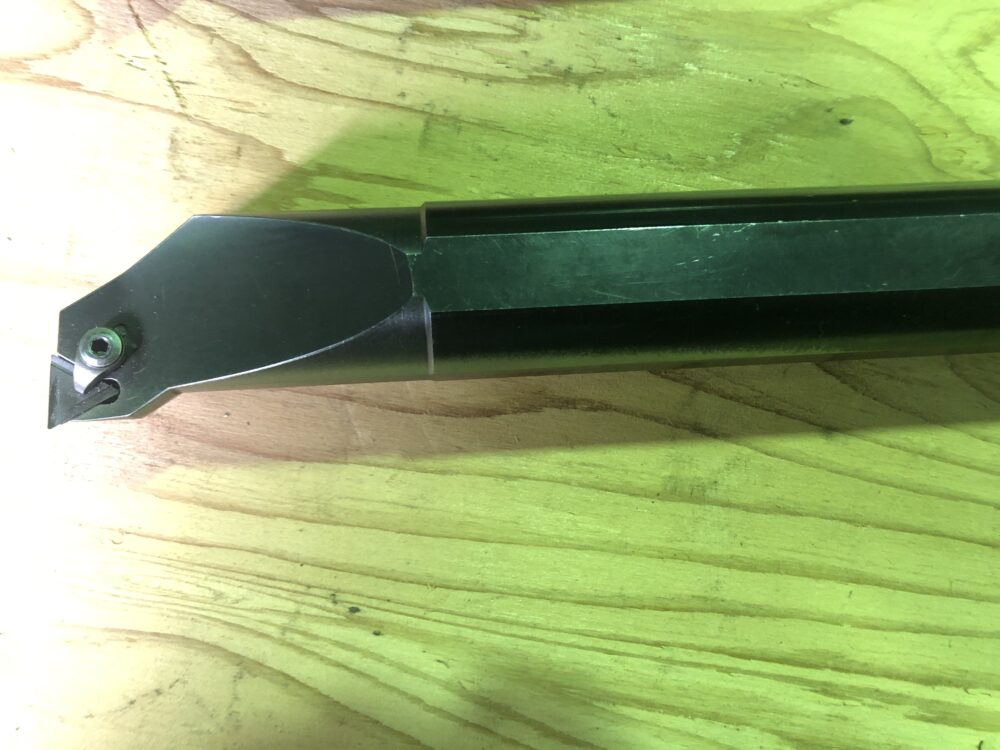
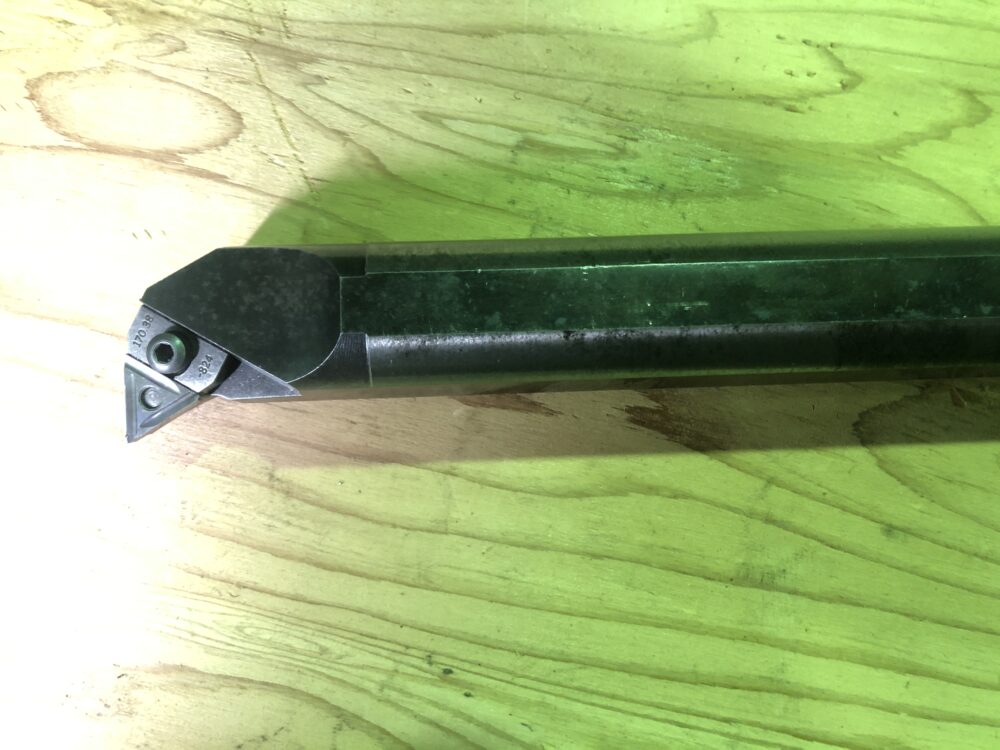
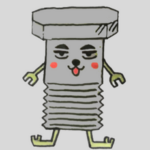
現場📋
※1ノギスでボーリングバーとチップの長さを測定して確認します。自信が無い人は、メーカーのカタログに最小加工径が記載されています。
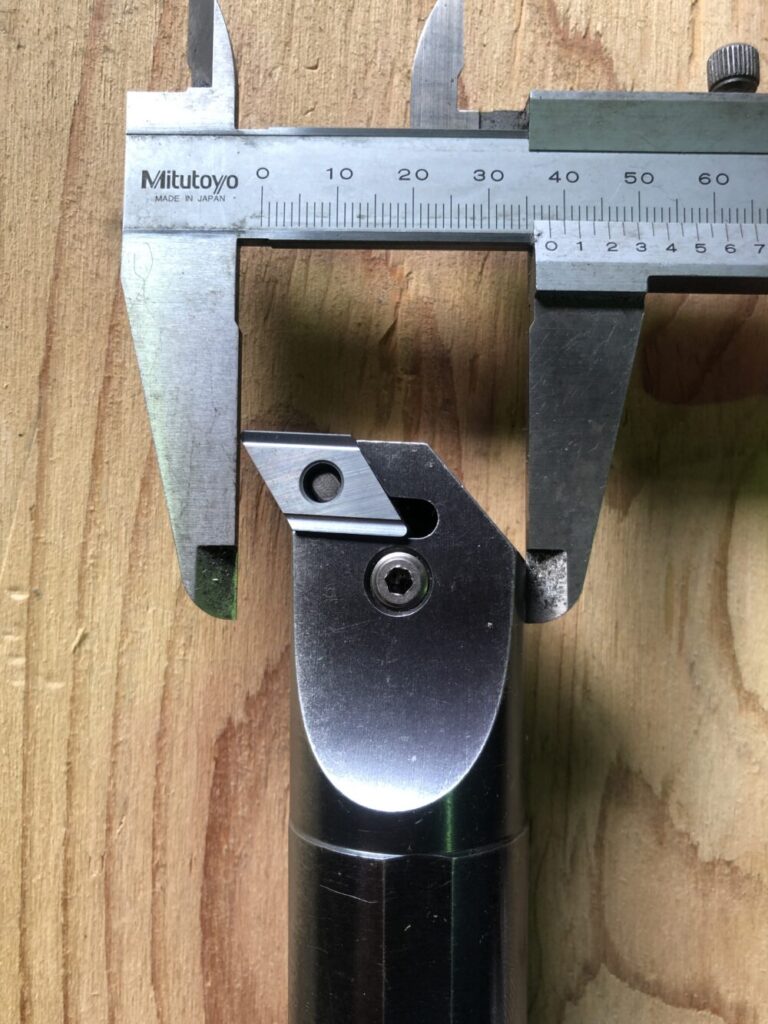
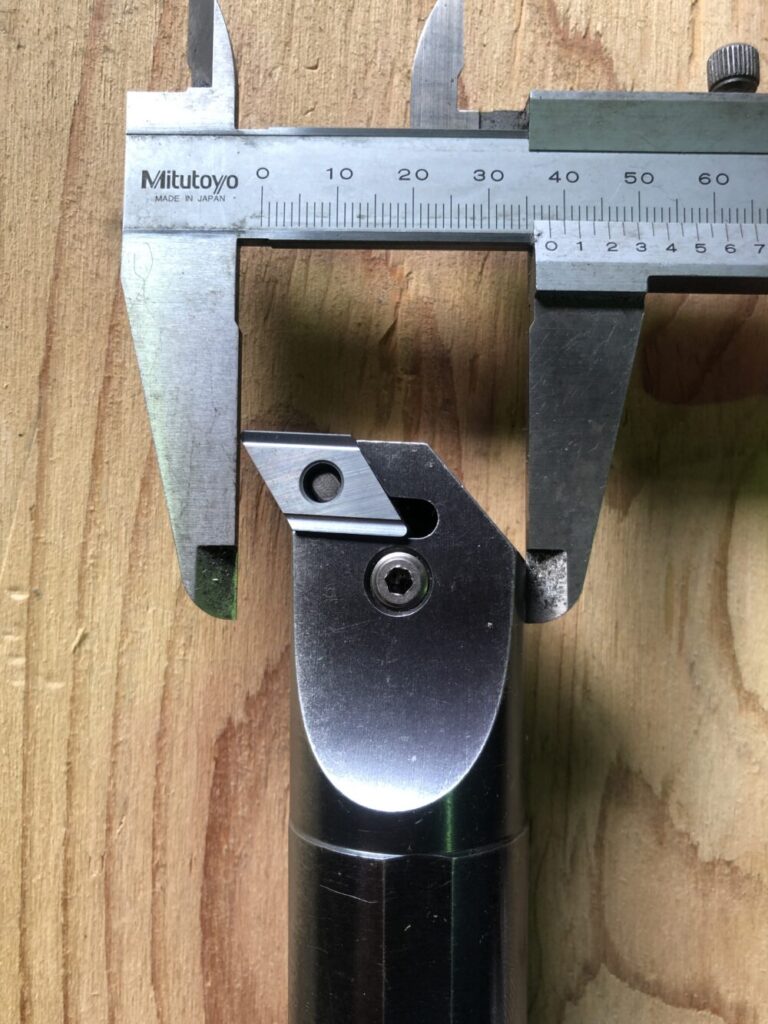
※中仕上げと仕上げは同じボーリングバー、チップでも大丈夫です。
注意事項としてチップに勝手がある場合は正回転の場合、右勝手のボーリングバーにはL(左勝手)のチップを使う。逆回転の場合、左勝手のバイトにR(右勝手)のチップが付きます。
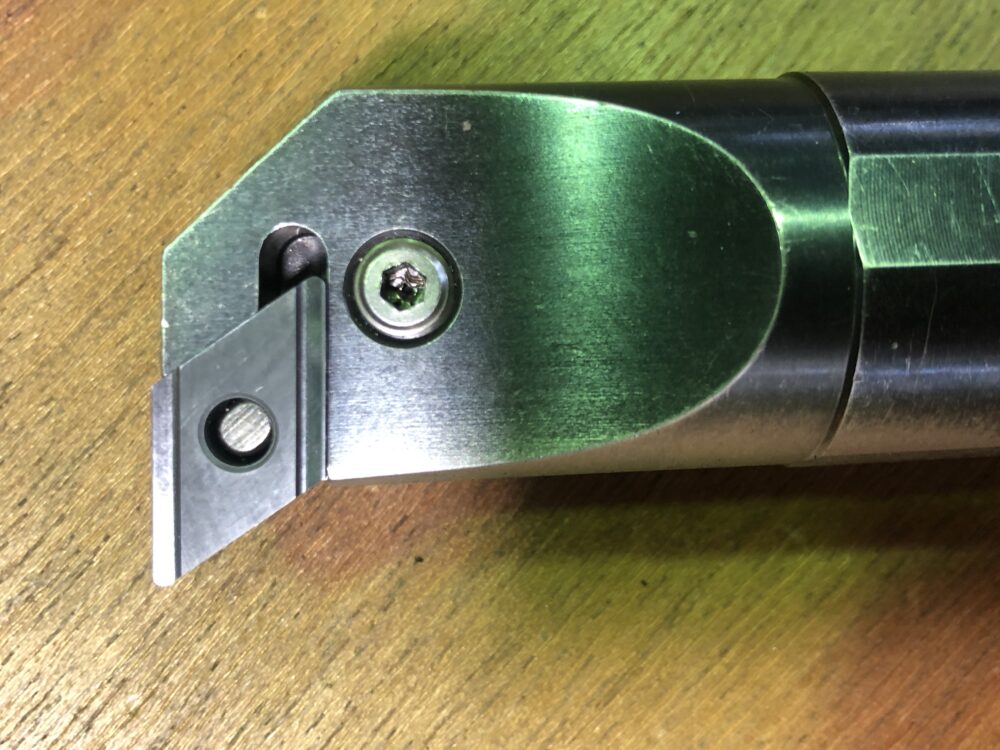
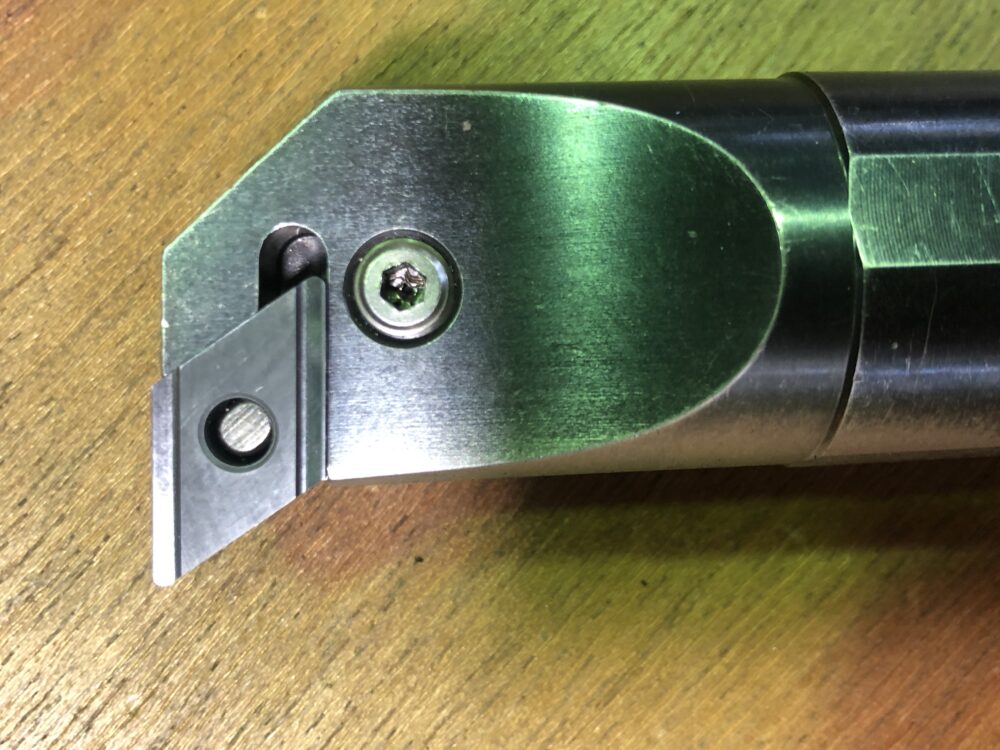
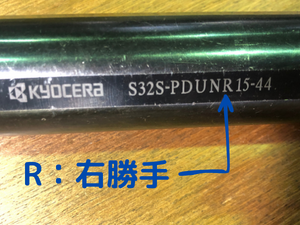
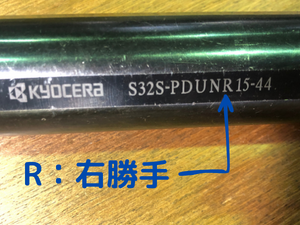
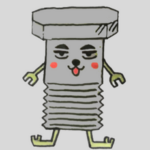
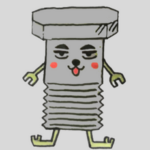
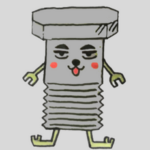
現場メモ📋
外径切削・・・正回転の場合、右勝手のバイトにはR(右勝手)のチップを使う。逆回転の場合、左勝手のバイトにL(左勝手)のチップが付きます。ややこしいですが間違えると速攻でチップが欠けるので、注意が必要。
3.切削条件の設定
切削条件の設定は、内径加工のにとって重要です。適切な切削条件を設定することにより、切削効率と仕上げの品質が変わってきます。以下は切削条件の設定に関するポイントです。
- 主軸の回転数:
旋盤の回転速度は、切削速度に影響を与えます。材料の硬度に合わせて適切な回転速度を設定し、切削効率をなるべく向上させましょう。 - 切削速度:
回転数と切削速度には関係あります。メーカーの推奨切削速度を参考にしましょう。
もっと詳しく知りたいお方は↓↓切削速度、回転数の関係に詳しく書いてあるので参考にしましょう。 - 送り速度:
送り速度は、内径の荒加工時には切りくず処理に多大に影響します。最適な送り速度を見つけ出しましょう。内径の仕上げ加工には、表面粗さを考慮して設定します。 - 切削液:
切削時に冷却液や潤滑剤を使用する場合、十分刃先に当たるように設置します。切りくずの処理にも非常に重要です。


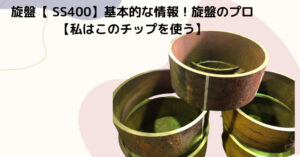
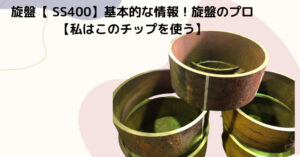
4.内径加工の手順の詳細
4.1. 材料の穴加工
穴開けは、内径加工の一つです。旋盤では、中心にのみ穴を開けることが可能です。
まずはハイスドリルで穴を開けます。超硬ドリルやスーパードリルは加工時間は、速くなるのですがトラブルがハイスドリルよりは多いので慣れてから使うようにしましょう。
4.2. 内径の荒加工
内径の荒加工は、穴の直径を大きくするための方法です。穴の直径を広げる必要がある場合、この加工方法が使用されます。
基本的に中心から均一(切り込み量)に材料を削り取っていきます。穴を広げると言う人もいます。
- チップの選択:
荒加工には刃先の丈夫な物を選定します。これにより、素材をバリバリ削り出すことができます。 - 切り込み深さ(切り込み):
荒加工はなるべく大きく取ります。一般鋼は2.5㎜くらいは問題無く削れます。 - 切りくずの除去:
内径の荒加工で厄介なのが、切りくずの処理です。遠心力が加わるので、内部に溜まってしまいます。棒で切りくずを出すか、切削液で処理しましょう - 回転速度と送り速度:
適切な回転速度と送り速度を設定します。荒加工は効率も求められます。チップの摩耗具合と機械剛性を考えて条件を設定します。切りくずがカールする場合は、送りを速くすると切りくずがカールしないようになります。
4.3.内径の中仕上げ加工
単品ものや数ものの1品目の場合、仕上げと同じ条件で1回中仕上げを行います。
仕上げと同じ条件で削る理由は、切削抵抗など色々な力を一定にすることで、寸法を出しやすくするためです。
※慣れないうちは2、3回くらい中仕上げをして寸法出しを慎重に行った方が良いでしょう
NC旋盤で、数ものを自動運転で加工する場合の時、中仕上げは要りませんが、精度物であれば中仕上げを1回入れるだけでも安定して品質の良い品物を作れます。
- 工具の選択:
中仕上げ加工には、基本的には仕上げバイトと同じ物を使いましょう。精度物で、品質を安定させたい場合は仕上げ加工用と中仕上げ用を分けます。 - 回転速度と送り速度:
正しい回転速度と送り速度を設定します。送り速度は面粗度に関わってきますので、面粗度を考慮して設定しましょう。なるべく仕上げ加工と同じ設定にしましょう。 - 切り込み深さ(切り込み):
中仕上げ加工では、荒加工よりも浅い切削深さが設定され、基本的には仕上げの取り代(0.4~0.1程度)と同じにします。
4.4. 表面仕上げ加工
仕上げ加工は、穴の内部表面を綺麗にします。ベアリングが入ったり、軸が入る場合が多いので、表面粗さと狙った寸法を確保する必要があります。
- チップの選択:
仕上げ加工には、迷ったらサーメットのチップを使いましょう。サーメットは構成刃先が付きにくく、高速切削が可能です。欠点として刃先に熱がこもりやすく、母材の材質が硬いので超硬よりは欠けやすいです。
母材が硬いので摩耗には強いです。 - 回転速度と送り速度:
回転速度は速いほうのが仕上がりは綺麗になります。慣れれば感覚で解りますが、慣れない内は推奨切削条件を確認しましょう。 - 切削深さ:
仕上げ加工では切り込み(0.1~0.4程度)は小さくしましょう。中仕上げをしている場合は、基本的には中仕上げと同じ切り込みにしてください。
5.内径加工の応用
5.1. ネジ切り加工
内径ねじの用途
- ナット
- 締結部品の固定
- パイプの接続(管用テーパーねじなど)
加工手順
①穴あけ
②内径加工
③内径ねじ切り
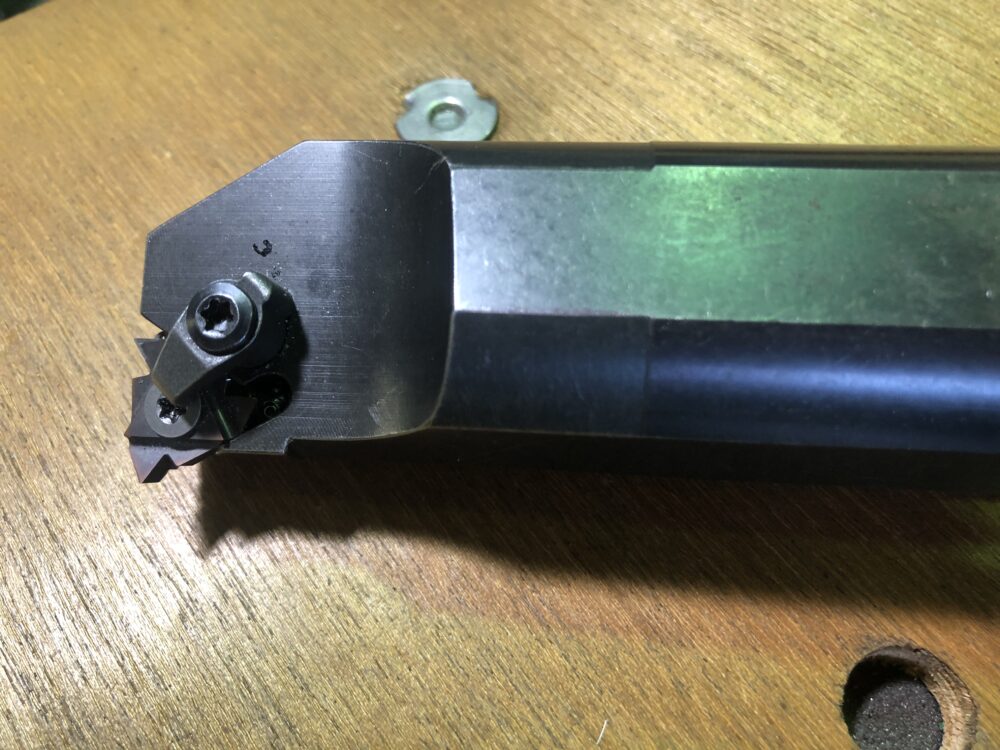
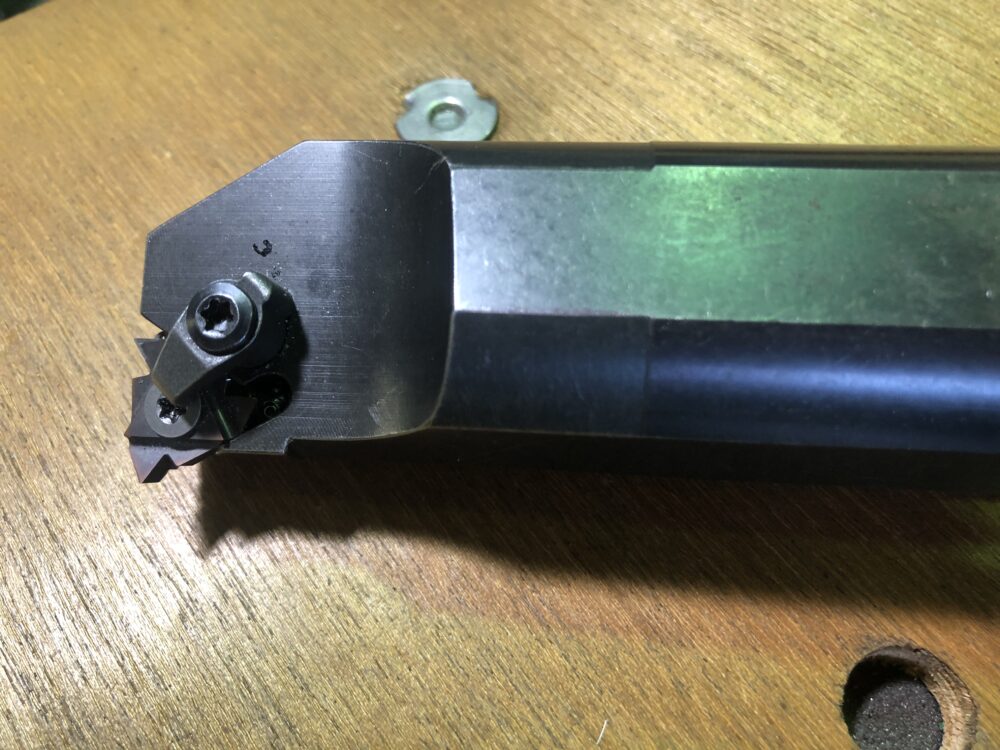
5-2.溝入れ
内径溝の用途
- Oリング溝:Oリングを保持するための溝
- ネジの逃がし
加工手順
①穴あけ
②内径加工
③内径溝入れ
5.3小径の内径加工する際の工具
スローアウェイバイトでは、チップを小さくするには限界があるため小径用にスティックバーという工具があります。
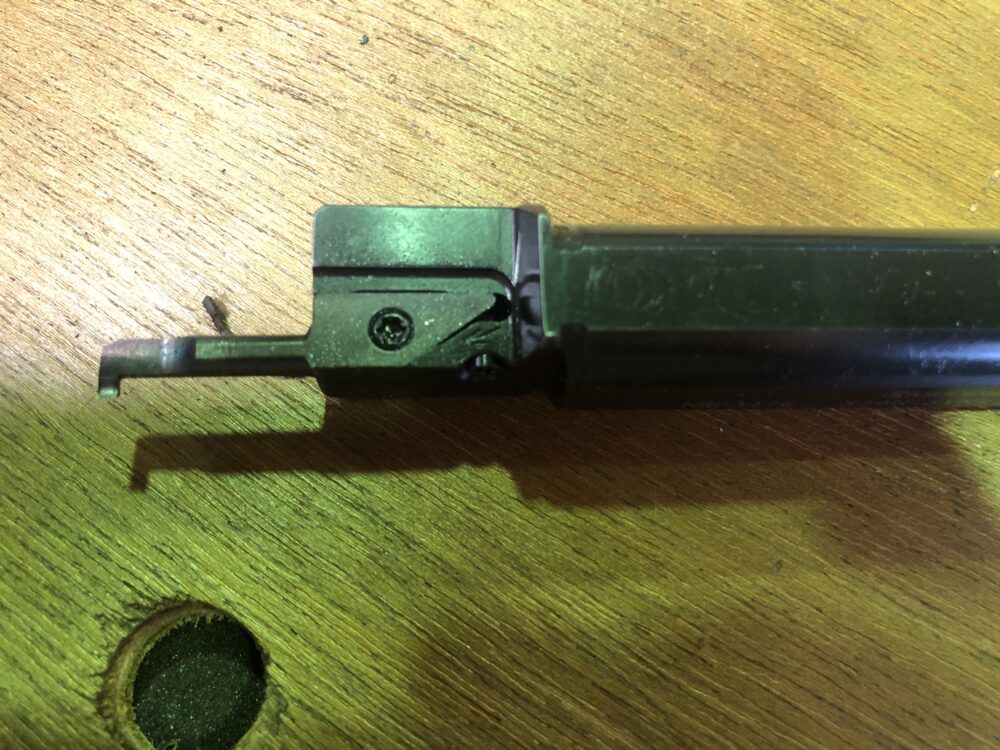
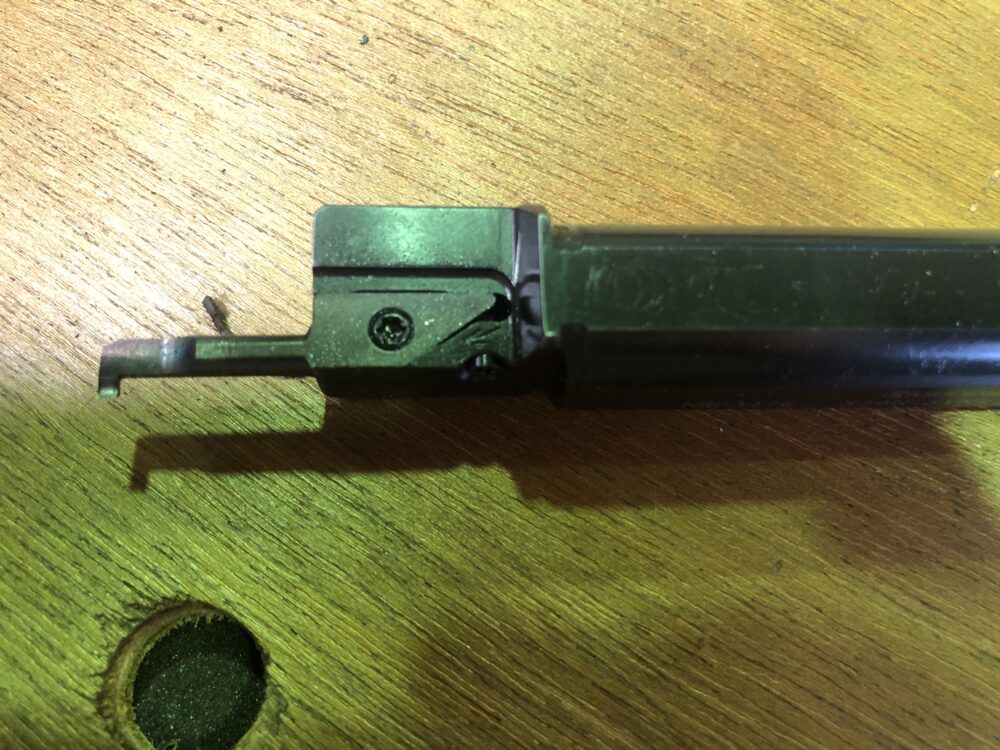
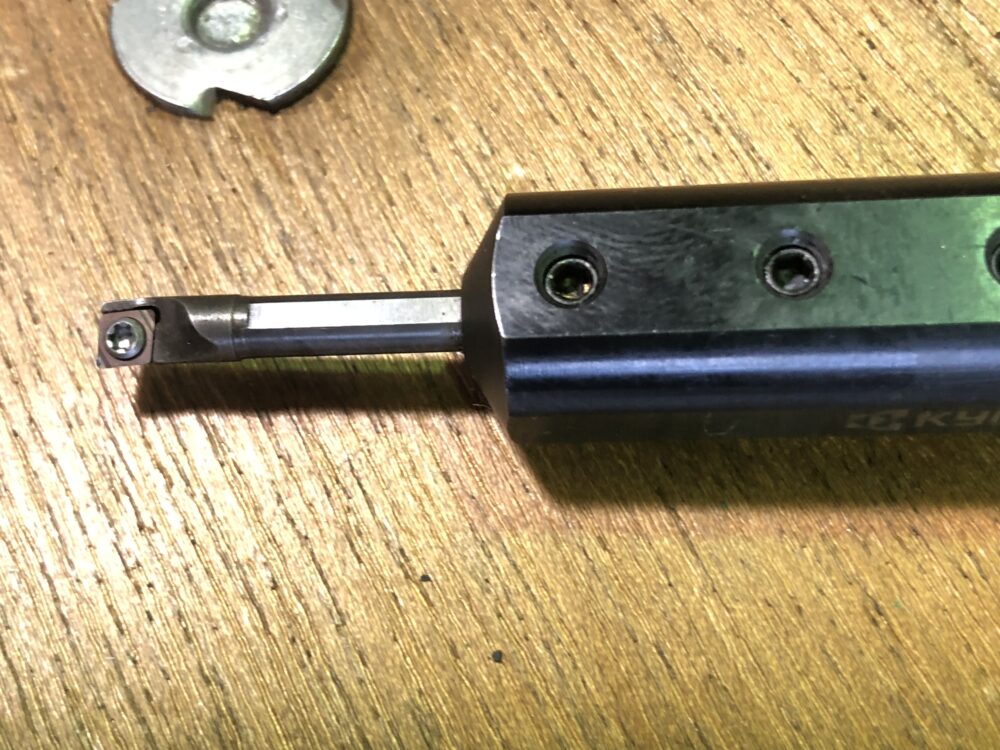
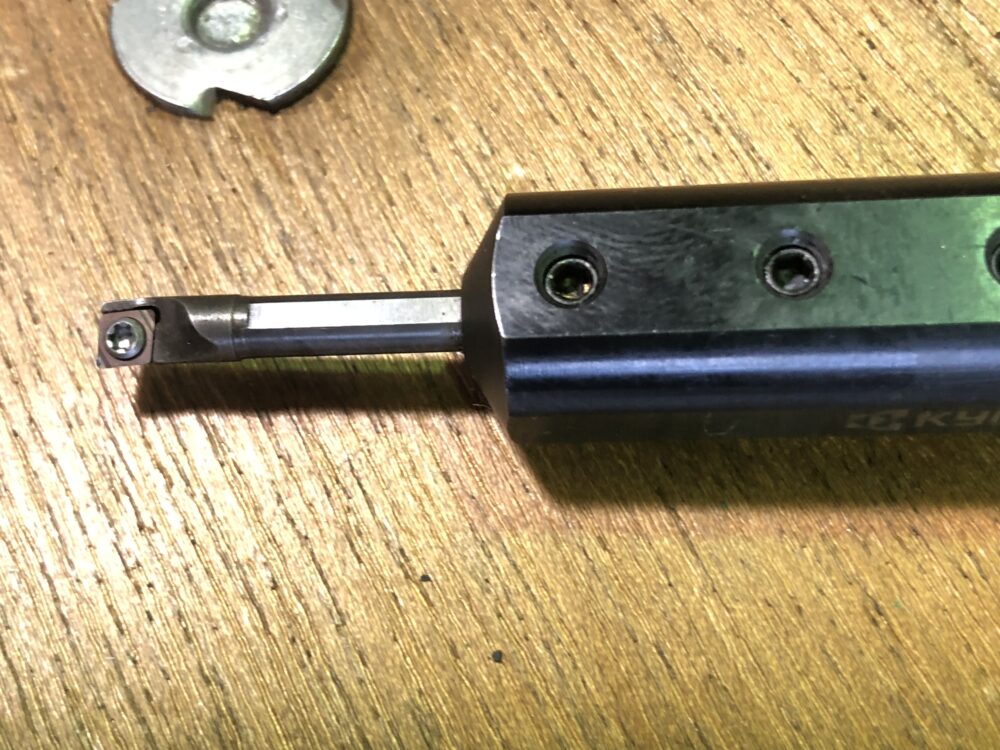
5.トラブルシューティング①:内径加工の切りくず処理
内径加工の難易度を上げている要因に切りくず処理があります。
切削した切りくずが遠心力により排出されないからです。
切りくずを切断する方法
まず考えなければならないのが、切りくずを切断させて、パラパラにすることです。カールしたままですと
排出させるのは難しいです。
切りくずを切断する方法として有効なのが、チップブレーカーを選定して切りくずをパラパラにすることです。
また送りを上げることも有効です。
振動切削という手法もあります。これは機械によっては使えないので補足です。
切りくずがカールしやすい難削材にはうれしい機能ですね。
切りくずを排出させる方法
切削液を十分にかけ、切りくずを排出させることが可能です。
また、切りくずが排出しきれなくても、ボーリングバーの選定で傷が付きにくい形状のものもあります。
チップ、ボーリングバーと製品の表面に隙間があったほうのが、内径加工時に傷がつきにくくなります。
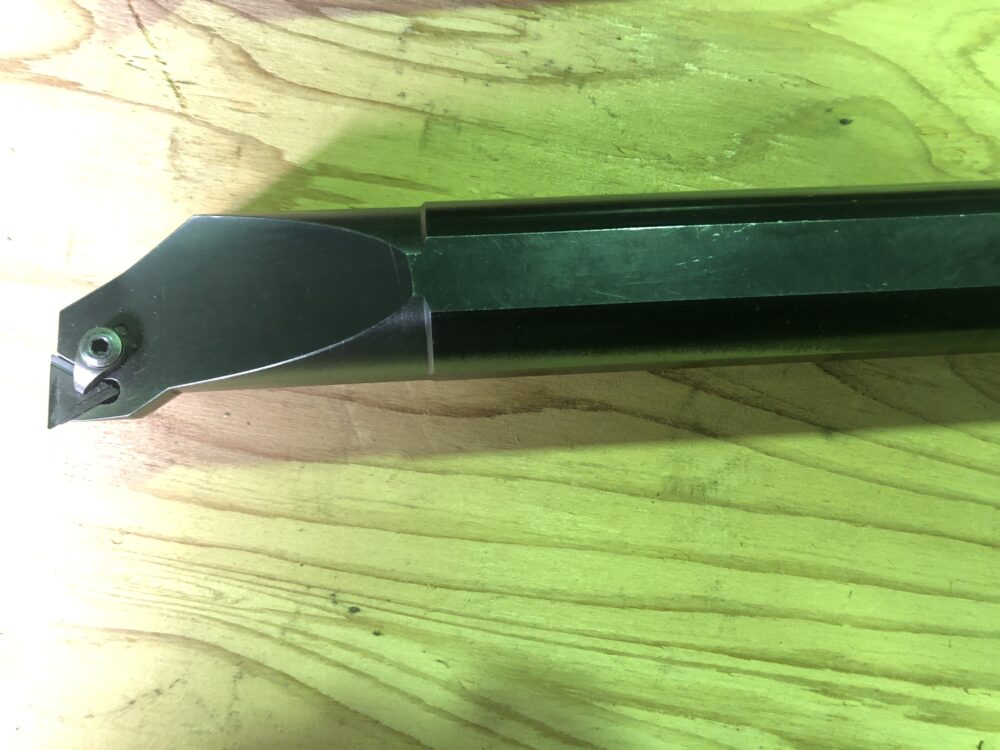
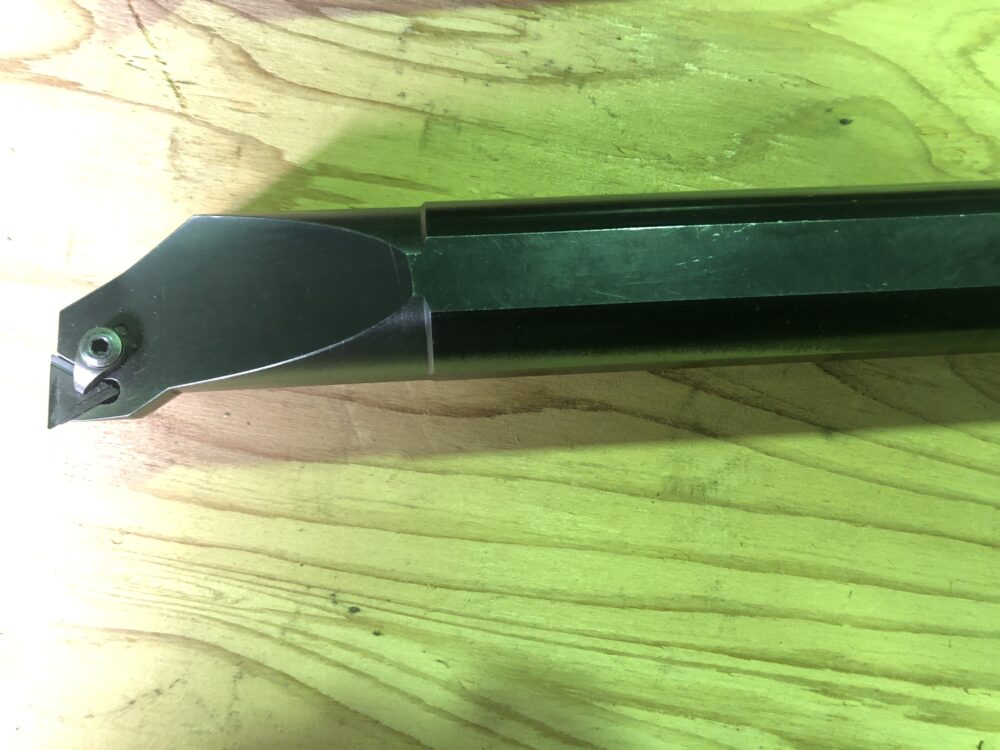
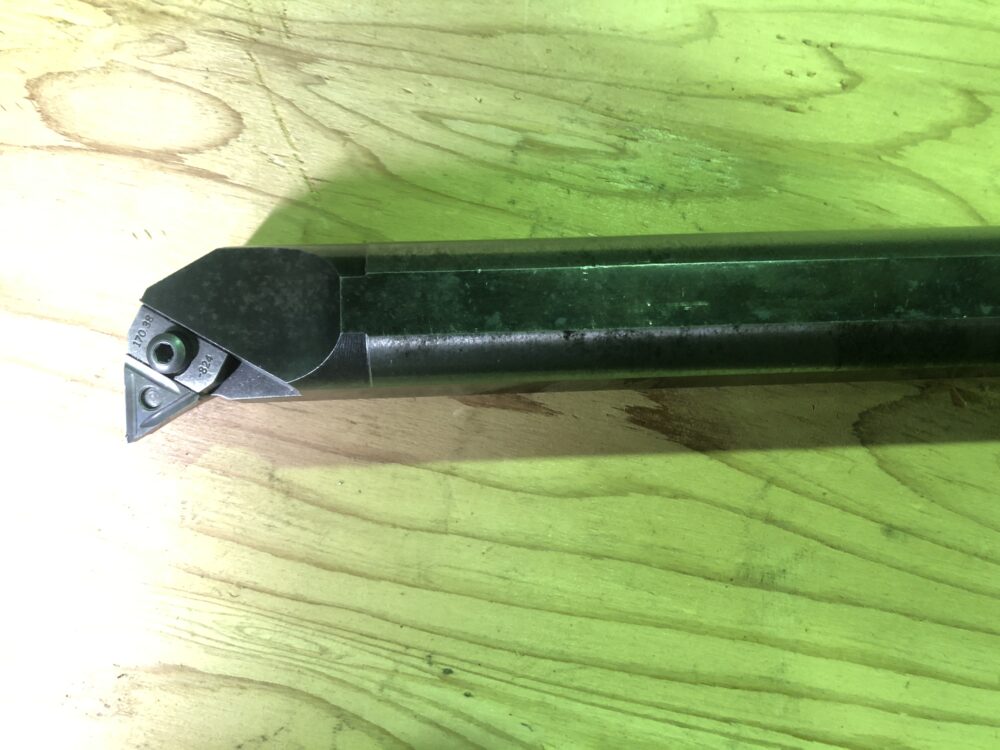
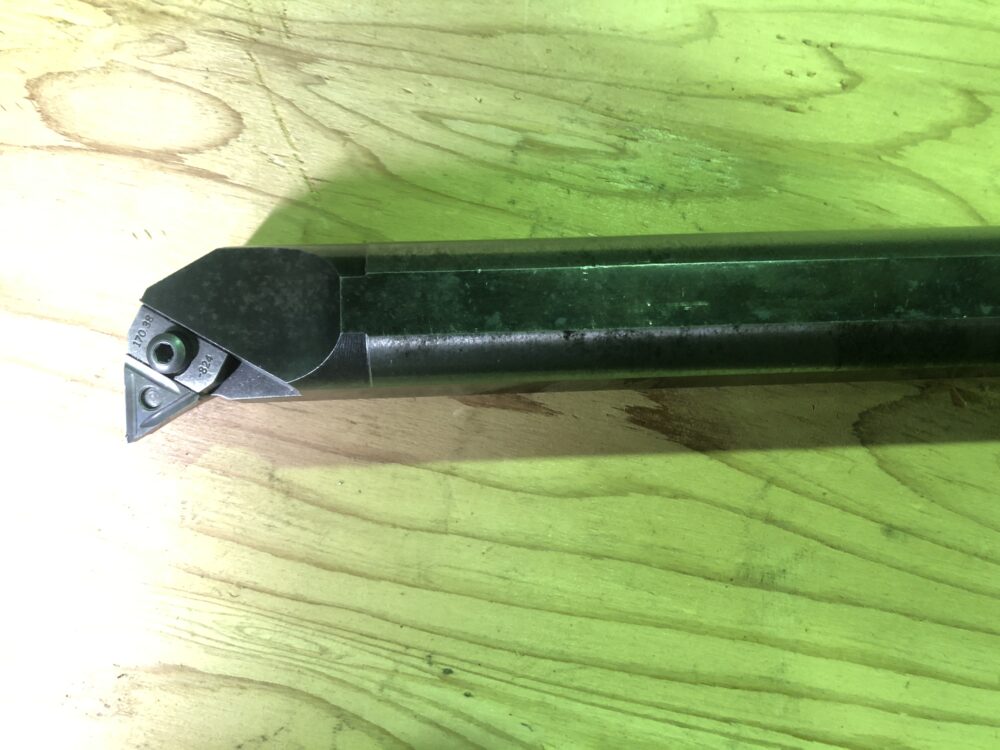
6. トラブルシューティング②:経験から得た内径加工のびびり対処法8選
①内径はシャンクの突き出し量が長いとビビりやすいです。短くできるならば、出来るだけ短くしましょう。
②シャンクを出来るだけ太くする
③刃先の心高さを中心より少し低くする。(参考書を参照)
④回転数(切削速度)を低くする。
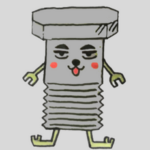
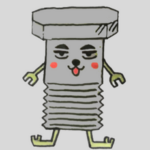
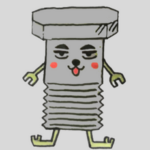
現場メモ📋
ねじ切りや溝入れの場合などはハイスを使うと切削速度を低くても綺麗に仕上がるし、ビビりも抑えることができ、有効です。
⑤超硬のボーリングバイトで加工します。
⑥マグネシウム製のスリーブを自作したり、スリットを入れたホルダーを作ったりしてクランプ方法を考えます。
⑦自作のボーリングバーを作る(基本的にはボーリングヘッドが軽いほうのがびびりは抑制できます)
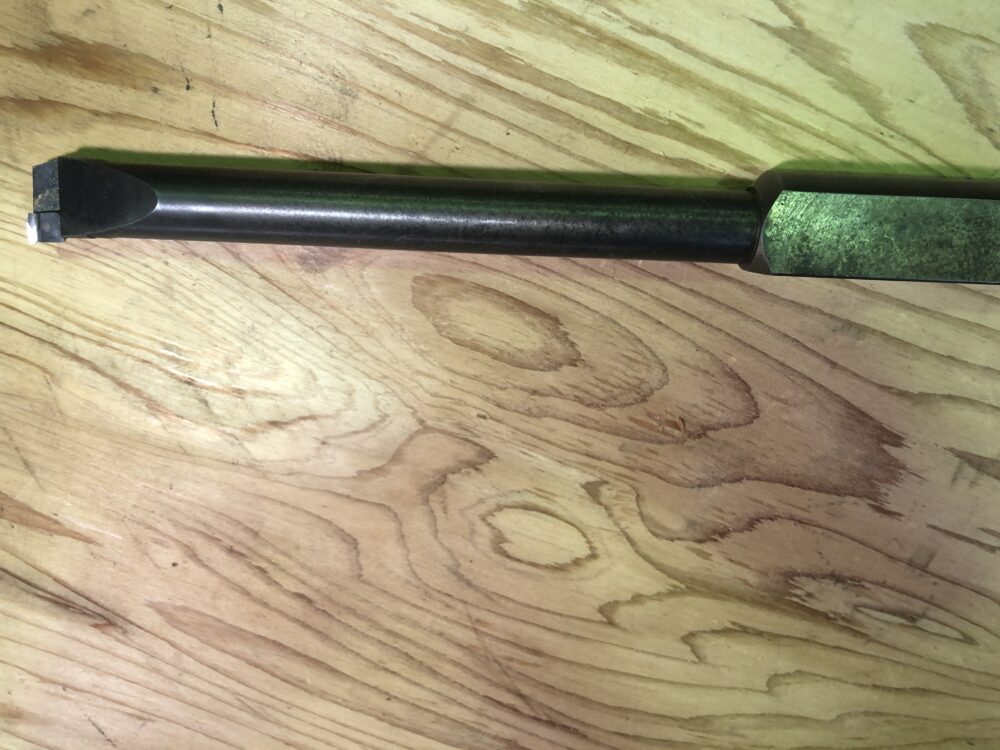
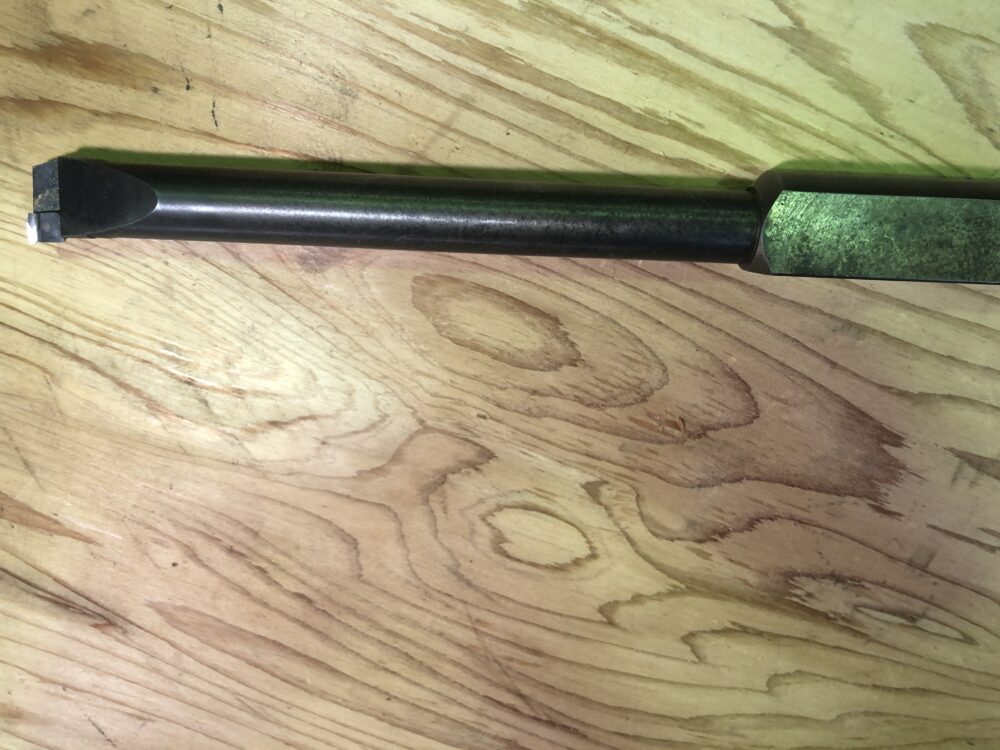
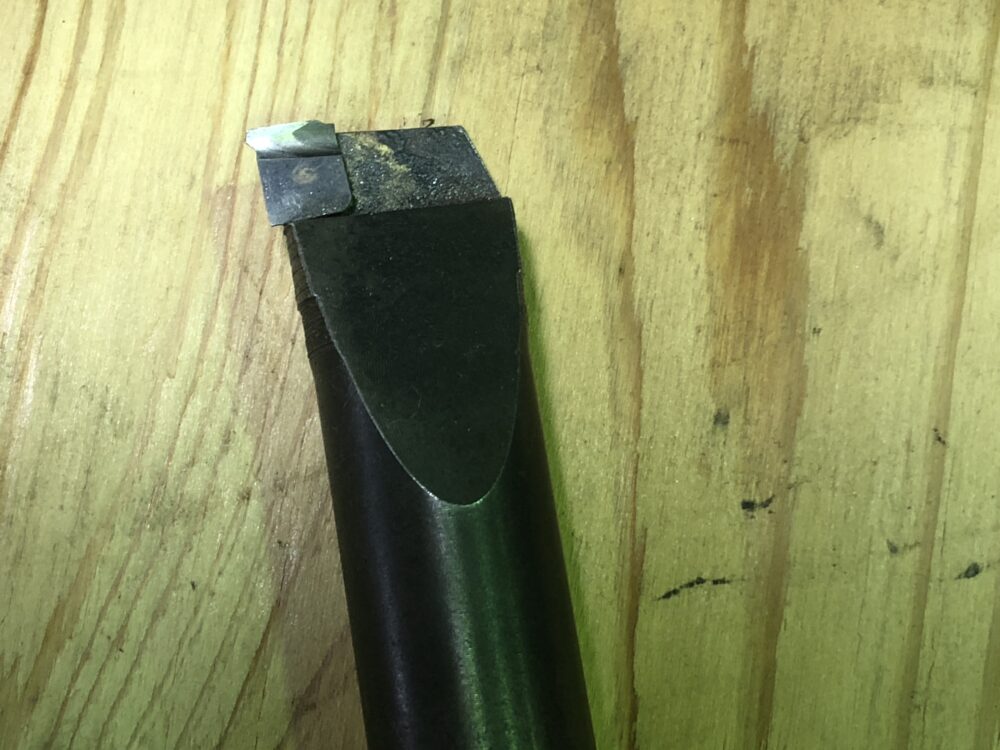
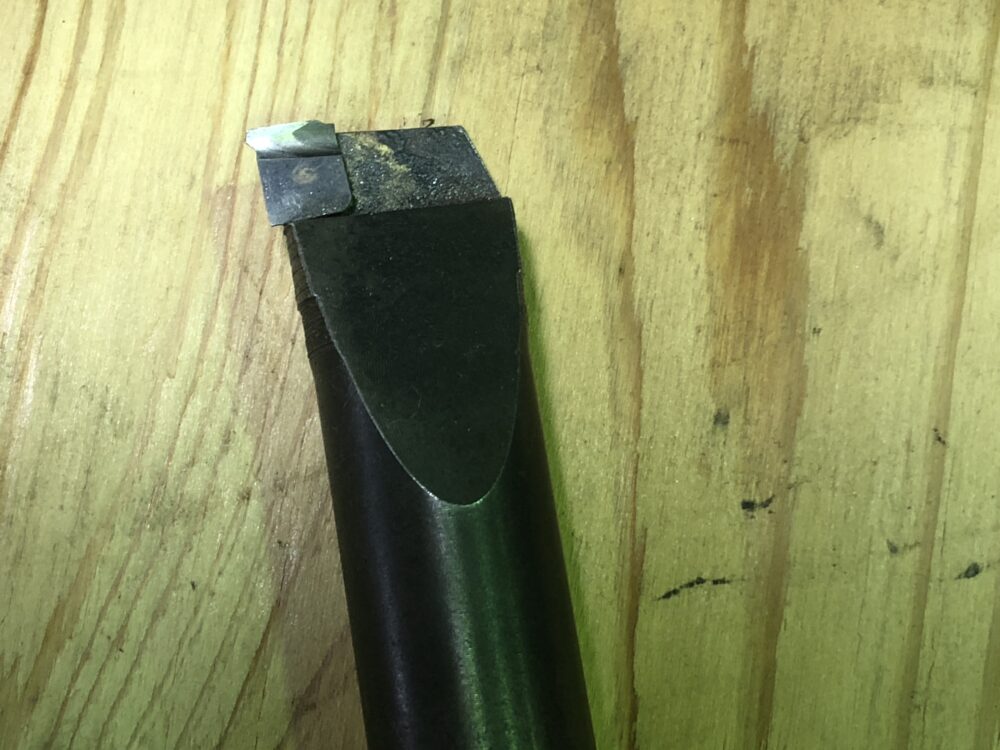
⑧最終手段は防振バー(ダンパー式)で加工する(最強です)
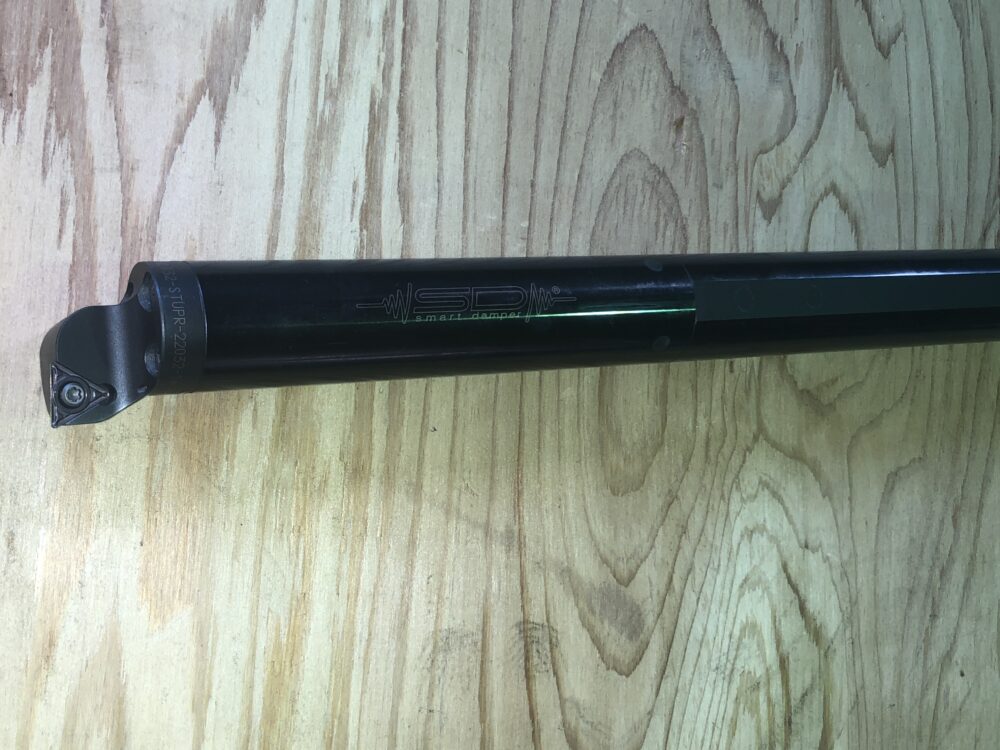
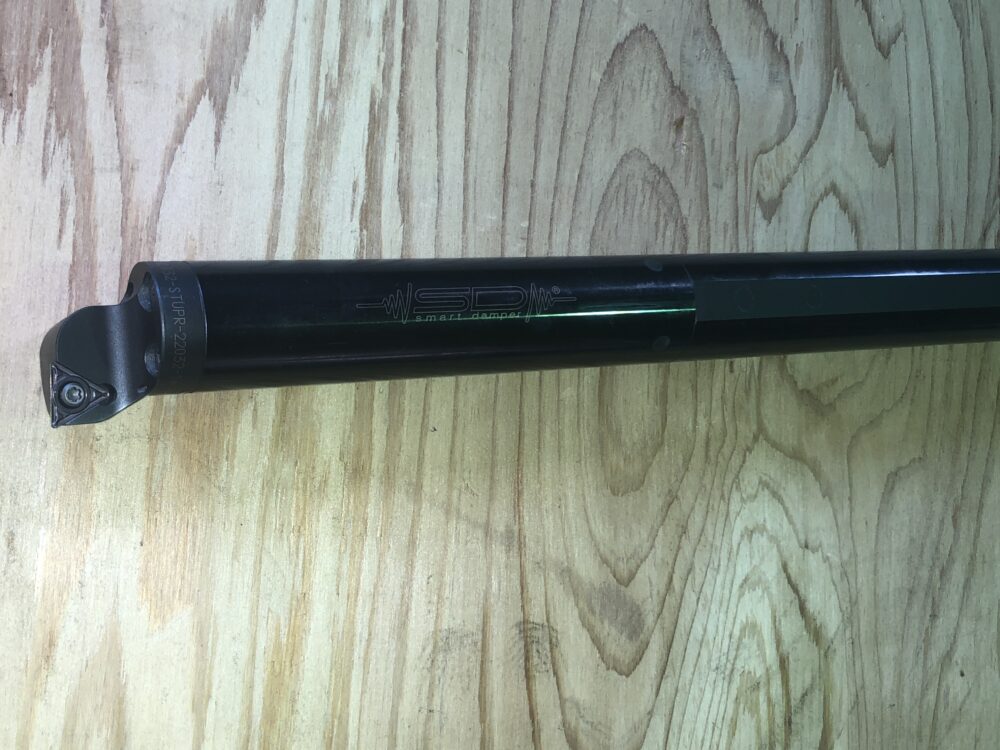
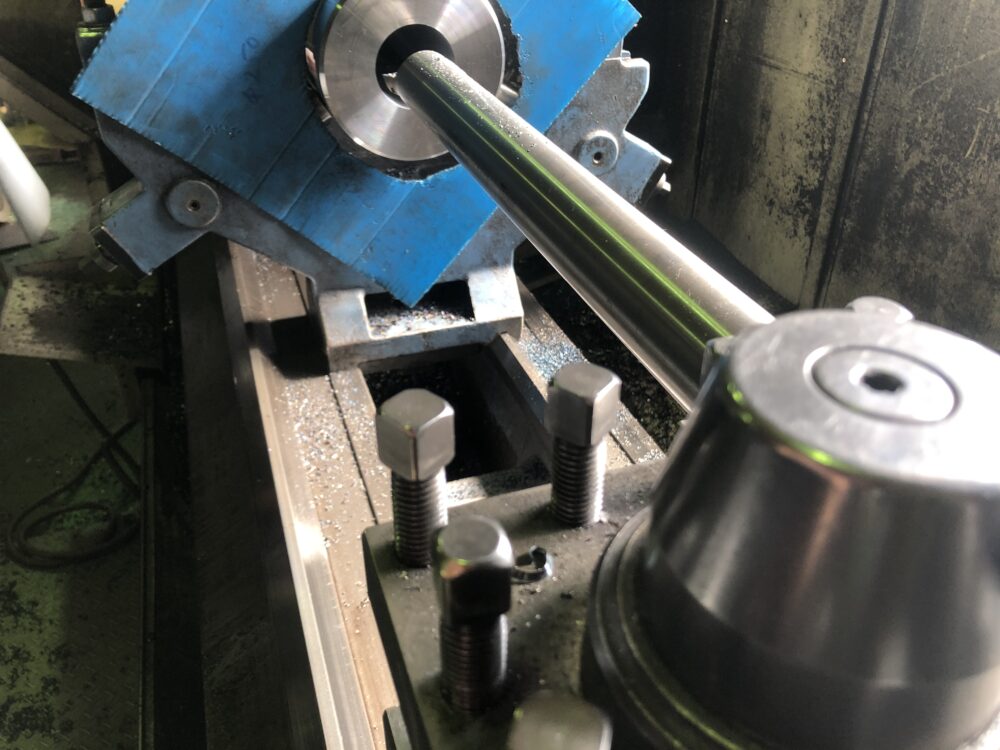
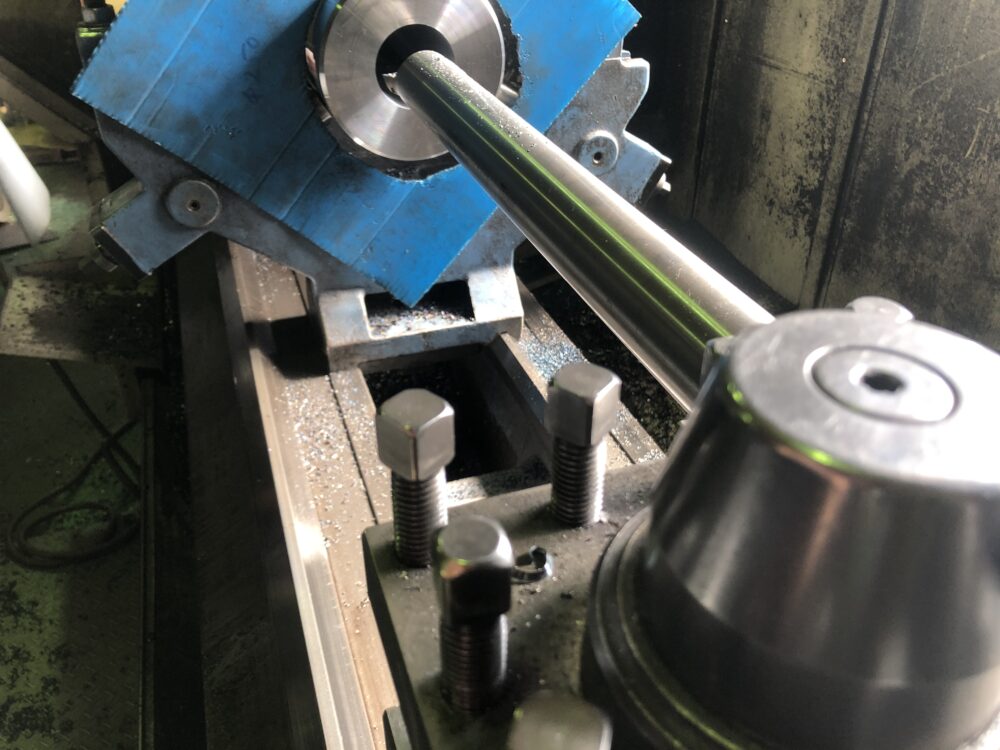
7.まとめ
内径加工は、加工の難易度が高く、外径や端面切削よりも多くの問題が発生します。内径加工には、以下の要点を押さえることが重要です。
工具の選定:
内径加工に適した工具を選ぶことが重要です。 材料、穴のサイズ、仕上げ要件に合わせて正しいなボーリングバーとチップを選びます。
切削条件の設定:
主軸の回転数、切削速度、送り速度などの切削条件を正確に設定する必要があります。これは切削効率と品質に大きな影響を与えます。
加工手順:
内径加工は一般的に穴あけ、荒加工、中、仕上げの手順で行われます。荒加工では、穴を拡大し、中で仕上げ寸法を整え、内径仕上げでは表面を仕上げます。
これらの手順に従って高品質な部品を製造できます。
トラブルシューティング:
内部処理において、ビビリ(振動)、切りくず処理の問題が発生することがあります。これらのトラブルに対処するために、切削速度の設定、刃先の形状、適切なツールの選択、突き出し量など適切な方法を知っておくことが重要です。
以上のことを踏まえて安全に注意して、トライしてみましょう
コメント